How Disney uses digital twins to maintain its most innovative rides
Ben draws on his professional expertise and personal love of theme parks to explore how Disney is solving problems before they even exist.
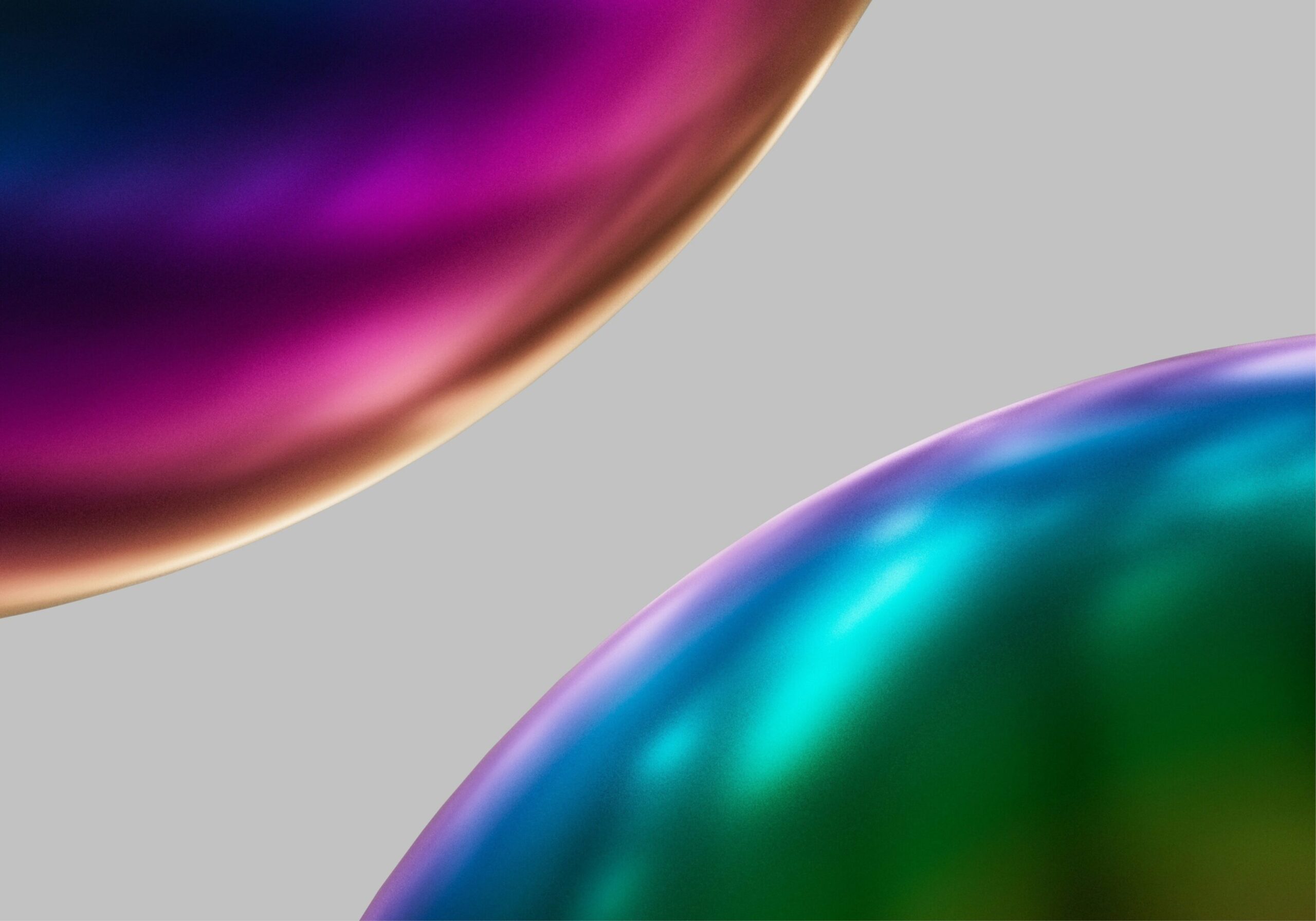
Disney’s Imagineers – the name Disney gives to members of its creative team – pride themselves on designing attractions that are the first of their kind. But when you’re building a never-seen-before ride, you have to contend with never-seen-before faults
Frequently replicated rollercoaster models such as Bollinger & Mabillard’s inverted coaster – think Nemesis at the UK theme park Alton Towers – have decades’ worth of operating history behind them. They’ve failed and been fixed so many times, maintenance teams know exactly what issues to look for and how to respond.
But how do you effectively maintain a ride with no operating history? And minimise downtime for the approximately 17 million guests who visit your most popular parks every year?
Disney has turned to a technology I often write about for Radix clients: digital twins.
A quick guide to digital twins
Digital twins are virtual replicas of physical objects, processes, people, or systems that are used to simulate real-life behaviour.
They’ve been used to model urban spaces for years, integrating real-time data from IoT (Internet of Things) devices and meteorological organisations to simulate everything from weather events to the movement of people and traffic.
In heavily populated locations, such as Los Angeles, city planners use digital twins to simulate specific areas, which allows them to create realistic roadmaps for decarbonising buildings. The technologically advanced SoFi stadium has its very own digital twin, enabling event organisers to better understand the experience of attending a game or a concert and design safer, more sustainable, and more enjoyable events.
And now, Disney is using digital twins to better understand some of its most innovative ride systems and deliver proactive maintenance that ensures smooth operations.
Keeping maintenance on track for trackless ride systems
Many of Disney’s latest attractions use trackless ride systems, with self-driving vehicles that follow a virtual path.
Imagineers have been experimenting with trackless elements in Disney’s rides for decades. Its iconic 1994 attraction Tower of Terror in Disney Hollywood Studios deviated from the traditional “drop tower” format, using trackless elevator cars to exit the shaft structure and send the carriage floating forward onto another plane. (It’s not the easiest thing to explain; thankfully, there’s a video here.)
Today, these ride systems are significantly more complex. Its newest attractions – like Tokyo Disney’s Beauty and the Beast – involve multiple cars navigating the “showrooms” simultaneously, in sync with hundreds of animatronics and effects, to create a seamless flow and tell a seamless story. (Again, see for yourself.)
In such attractions, achieving something close to mechanical perfection is vital to the illusion; seeing just one animatronic fail during a ride-through could be enough to break a guest’s immersion.
This makes effective maintenance essential. So how do you manage those countless components and potential points of failure, and plan for problems that no one in the world has experienced before?
Proactive maintenance in a digital environment
Working with its analytics partner Hitachi Vantara, Disney has created digital twins for two of its most advanced attractions to date – Star Wars: Rise of the Resistance and Mickey and Minnie’s Runaway Railway.
These digital twins are paired with IoT sensors throughout the attractions. In Rise of the Resistance, the sensors can capture up to 40,000 data points at once.
Disney’s data management and analytics platform ingests millions of data points from these sensors every hour, uses AI to assess the condition of each ride component, and predicts when engineers should schedule maintenance – even as guests continue to cower away from Kylo Ren’s lightsaber or plummet over a waterfall with Mickey and Minnie Mouse.
But the real Disney magic happens in the digital twins. The digital twins take the data captured from an attraction’s IoT sensors and feed it into highly detailed simulations, identical to the attractions’ complex mechanical and electrical systems.
These simulations replicate everything down to the smallest details, from the ride systems themselves to the lifelike audio-animatronic figures that populate the sets. And in parts of the attractions where Disney can’t place sensors, the digital twin’s predictive AI models fill in the gaps.
Disney’s engineers gain a real-time understanding of the condition of each ride system, including the velocity, acceleration, and torque experienced by ride components. Crucially, they also let engineers model never-seen-before faults and plan effective maintenance strategies.
As you can imagine, all this helps to minimise downtime for these massively popular attractions. Another tactic Disney’s pioneered to keep the lines flowing is the introduction of “B-plots”. When an attraction’s engineers spot a specific component in the ride’s digital twin that isn’t working as it should – such as the physical animatronic of Mickey and Minnie in a hot air balloon – they can trigger the attraction’s B-plot.
This alternative mode removes the animatronic from the ride sequence and replaces it with a similar animation on a screen. Most guests won’t notice there’s even been a change, while simultaneously, engineers can work on the animatronic as the ride continues. It’s something that wouldn’t be possible without the free movement of a trackless ride system or the real-time understanding provided by the attraction’s digital twin.
There’s no challenge too big or small for digital twins
Just as its innovative ride systems inspire other ride designers, Disney’s use of digital twins is sure to be taken as a blueprint by other theme park operators.
Keeping our theme park rides flowing smoothly might not be the most pressing challenge facing the world right now, but stories like these are testament to the technology’s remarkable versatility.
It’s also nice to think that, in some bright future when I leave my low-carbon house, travel on a perfectly punctual train through a sustainable city, and arrive at my local theme park, I’ll find a new, seamlessly immersive ride, that once again subverts my expectations and blows my mind.
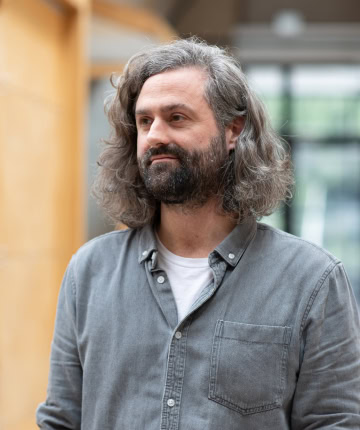
Kieran Haynes
Head of Copy
Kieran’s versatility as a content writer and extensive B2B marketing experience often see him singled out by clients looking to push the creative envelope. As our Head of Copy, he provides scrutiny and support in equal measure, helping us to ensure everything we produce is the best it can possibly be.